Loctite 638 vs 648: Strength Comparison
Loctite 638 vs. 648: A Comparison
Understanding Retaining Compounds
Loctite 638 and 648 are both renowned retaining compounds used in various industrial applications. Retaining compounds, such as these, are designed to bond cylindrical fitting parts. By filling the space between components and curing to form a strong, precise bond, they ensure reliable assembly and performance.
Loctite 638 delivers the highest strength of all Loctite retaining compounds, making it ideal for heavy-duty tasks. In contrast, Loctite 648, with its ability to fill smaller gaps up to 0.15mm, is tailored for high-precision applications. These retaining compounds cure well on both active and passive metal surfaces without the need for a primer, providing versatility in various applications.
Application in High-Temperature Environments
Both Loctite 638 and 648 perform efficiently in high-temperature environments. These adhesives can withstand temperatures up to 180°C (355°F), making them suitable for conditions involving extreme heat. This resilience is essential for ensuring the durability and longevity of bonded assemblies in demanding industrial settings.
The temperature resistance and thermal stability of Loctite 638 and 648 make them effective solutions for applications subjected to continuous temperature fluctuations. The operating range for these products typically spans from -65°F to 300°F (-55˚C to +150˚C). However, high-performance grades are available to extend these limits, ensuring the specific requirements of each application are met.
For detailed guidance on their suitability for various uses, consider exploring our article on advantages and disadvantages of different retaining compounds.
Summary of Temperature Resistance
Product | Maximum Temperature | Typical Continuous Range |
---|---|---|
Loctite 638 | 180°C (355°F) | -65°F to 300°F |
Loctite 648 | 180°C (355°F) | -65°F to 300°F |
Both products are excellent choices for assembling parts in high-temperature environments. While Loctite 638 excels in heavy-duty applications, Loctite 648 is better suited for precise tasks with smaller gaps and faster curing times. For more insights on various adhesives’ performance in extreme conditions, check ge silicone.
Strength and Curing Characteristics
In comparing Loctite 638 and Loctite 648, understanding their strength and curing characteristics is essential for determining the best fit for various applications.
Shear Strength and Gap Tolerance
Loctite 638 offers the highest strength of all Loctite retaining compounds. It is suitable for heavy-duty applications, boasting a high shear strength of 31 N/mm² (Stickyn). This makes it the preferred choice for applications requiring the ability to fill larger gaps.
Compound | Shear Strength (N/mm²) | Gap Tolerance |
---|---|---|
Loctite 638 | 31 | Larger gaps up to 0.25mm |
Loctite 648 | 25 | Smaller gaps up to 0.15mm |
Loctite 648, while slightly lower in strength with a shear strength of 25 N/mm², excels in applications with smaller gaps. It can effectively fill clearances up to 0.15mm and is ideal for precision bonding tasks.
Cure Speed and Precision Bonding
When time is a crucial factor, Loctite 648 stands out with its quicker curing time, particularly on passive metals. This makes it a better choice for scenarios where rapid bonding is necessary.
Loctite 638, though superior in strength, may take longer to cure, which could be a disadvantage in time-sensitive applications. Its versatility in bonding through minor surface contaminants adds to its utility in various industrial contexts.
For detailed information on different bonding adhesives, you can visit our article on 1 part vs. 2 part epoxy.
Compound | Cure Speed | Best Applications |
---|---|---|
Loctite 638 | Slower | Heavy-duty tasks |
Loctite 648 | Faster (especially on passive metals) | Precision, smaller gaps |
In terms of precision bonding, Loctite 648 is advised for bonded heat shrink-fit and slip-fitted assemblies, applied with a twisting motion for optimal bonding.
For more tips and methods on adhesive applications, explore our articles on 3m 5200 fast cure and 3m weatherstrip adhesive.
Temperature Resistance and Operating Range
Maximum Temperature Performance
When comparing Loctite 638 and Loctite 648, temperature resistance is a critical factor, especially for applications in high-temperature environments. Both products exhibit impressive thermal capabilities, but there are some differences worth noting.
Loctite 648 is known for its high thermal resistance, making it suitable for continuous use at elevated temperatures. This compound is often recommended for heat shrink-fit assemblies, which require stable bonding performance under intense heat conditions. Loctite 648 can withstand a maximum operating temperature up to 355°F (180°C) (ConRo Electronics Ltd).
Loctite 638, on the other hand, also offers robust thermal resistance but is slightly less resilient compared to Loctite 648. It can handle maximum temperatures up to 300°F (150°C). This makes it well-suited for applications where high strength is required but the temperature conditions are moderately high.
Continuous Operating Temperature Range
The continuous operating temperature range of retaining compounds is another crucial element to consider. This metric determines how well the adhesive performs under prolonged exposure to a specific temperature range.
Loctite 648 is engineered for continuous high-temperature performance and remains effective within a broad temperature range. It maintains its structural integrity and bonding strength under extended exposure to temperatures spanning from -65°F to 355°F (-55°C to 180°C).
Loctite 638 offers a slightly narrower continuous operating range, performing effectively between -65°F to 300°F (-55°C to 150°C). While its thermal performance is commendable, it may not be ideal for applications requiring constant exposure to temperatures approaching the upper extremes of its operating range.
Compound | Maximum Temperature (°F) | Continuous Range (°F) |
---|---|---|
Loctite 638 | 300 | -65 to 300 |
Loctite 648 | 355 | -65 to 355 |
For more details on applications requiring thermal resistance, see our article on the advantages and disadvantages of different adhesive types.
By understanding the maximum temperature performance and continuous operating temperature range of Loctite 638 and Loctite 648, users can make well-informed decisions about which product best meets their needs, particularly for high-temperature environments. For certifications and chemical tolerances, refer to our section on upgraded features and improvements.
Industrial Applications
Heavy-Duty vs. Precision Tasks
When choosing between Loctite 638 and 648, it’s crucial to consider the specific requirements of your industrial application. Both retaining compounds offer distinct advantages, catering to different types of tasks.
Loctite 638: This compound is specifically designed for heavy-duty applications. It provides the highest strength of all Loctite retaining compounds and is suitable for bond gaps up to 0.25 mm. Loctite 638 is an excellent choice for applications demanding high durability and structural integrity, such as:
- Automotive shaft repairs
- Heavy machinery assembly
- High-load bearing connections
Loctite 648: On the other hand, Loctite 648 excels in precision tasks. It performs well with smaller gaps, effectively filling clearances up to 0.15 mm. It cures quickly on passive metals, making it a more efficient option when time is of the essence. Applications best suited for Loctite 648 include:
- Electronic device assembly
- Medical equipment manufacturing
- Precision tools and instruments
Compound | Strength | Gap Tolerance | Best For |
---|---|---|---|
Loctite 638 | High | Up to 0.25 mm | Heavy-duty applications |
Loctite 648 | Medium-High | Up to 0.15 mm | Precision tasks |
Compatibility and Surface Contaminants
Compatibility with different surfaces and the ability to handle contaminants is another important factor when selecting a retaining compound.
Loctite 638: This compound is formulated for use with all metals, and it cures effectively even in the presence of minor surface contaminants. This makes it versatile and reliable for a wide range of industrial scenarios where thorough surface cleaning might not always be feasible.
Loctite 648: While also compatible with various metals, Loctite 648 is particularly noted for its quick curing on passive metals, such as stainless steel or coated materials. Its ability to cure faster in such conditions makes it ideal for applications requiring swift handling and less downtime.
For more detailed guidance on selecting the right adhesive for your needs, explore our articles on advantages and disadvantages and 1 part vs. 2 part epoxy.
Surface Contaminants Handling:
- Loctite 638: Effective on slightly contaminated surfaces.
- Loctite 648: Faster curing on passive metals, handling minor contaminants well.
By understanding these differences, professionals can make informed decisions, ensuring robust, long-lasting bonds whether handling heavy-duty machinery or precise electronic components. For additional information on adhesive options and their industrial roles, read more about Barge Cement and 3M Super Strength.
Upgraded Features and Improvements
When comparing Loctite 638 and 648, understanding their upgraded features and improvements is essential. Each compound offers distinct advantages, particularly in areas such as temperature resistance and chemical tolerance.
Enhanced Temperature Resistance
Loctite 648 is specifically designed for high-temperature applications. This adhesive performs reliably at service temperatures up to 200°C (392°F), making it ideal for environments that experience higher temperatures (Stickyn). This characteristic makes Loctite 648 suitable for use in applications involving cylindrical fitting parts with small gaps up to 0.15 mm, particularly in precision tasks.
The standard continuous operating temperature range for LOCTITE anaerobic adhesives is -65°F to 300°F (-55°F to +150°C). However, the high-performance grades offered by products like Loctite 648 extend this range, which is beneficial for industries such as automotive and maintenance, repair, and operation (MRO) applications. Explore more about the 3m 5200 fast cure adhesive for comparison.
Product | Maximum Temperature | Standard Continuous Operating Range |
---|---|---|
Loctite 638 | 150°C (300°F) | -65°F to 300°F (-55°F to +150°C) |
Loctite 648 | 200°C (392°F) | -65°F to 300°F (-55°F to +150°C) |
Chemical Tolerance and Certification
Loctite 648 is known for its high resistance to various chemicals. Once cured, it offers strong resistance to gasoline, diesel, engine oil, water, glycol, acids, alkalis, and hydraulic fluid. This makes Loctite 648 an excellent choice for applications that require long-term durability in chemically harsh environments.
Certifications for chemical tolerance often ensure that the compound can handle rigorous industrial demands. For instance, Loctite 648 is recommended for bonded heat shrink-fit assemblies and for slip-fitted assemblies, adhering to manufacturer guidelines to achieve optimal performance. This makes it a versatile option for various industrial applications. Learn more about the advantages and disadvantages of different adhesives.
By examining these upgraded features and improvements, you can discern the best use cases for Loctite 638 and 648. For more detailed insights, consider the specific industrial applications and requirements that each product can address. This information helps to make an informed decision tailored to your particular needs in high-temperature and chemically robust environments.
Applications and Recommendations
Best Uses for Loctite 638
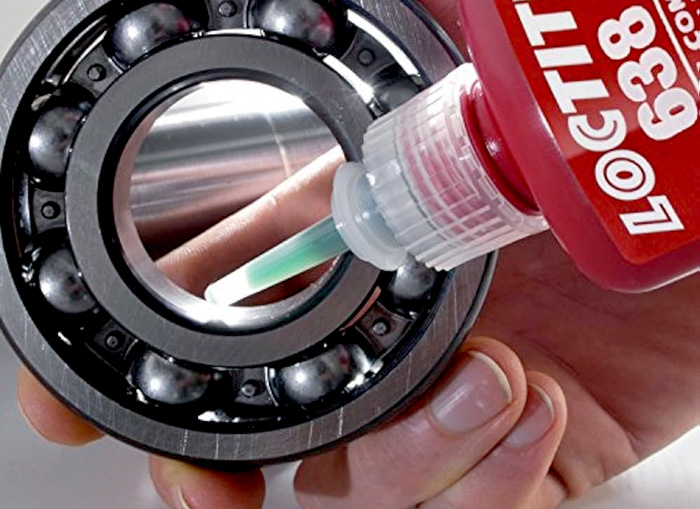
Loctite 638 is known for its superior high-temperature performance, making it well-suited for applications requiring robust strength in demanding environments. It operates effectively up to 180°C (355°F). This makes it an excellent choice for heavy-duty applications involving retaining compounds.
Key features of Loctite 638 include:
- High Temperature Resistance: Ideal for applications experiencing elevated temperatures.
- Gap Tolerance: Performs exceptionally well in applications with larger gaps.
- Heavy-Duty Usage: Suitable for retaining sleeves, bushes, and bearings in high-stress scenarios.
Applications where Loctite 638 shines:
Application | Characteristics |
---|---|
Retaining Sleeves | Strong resistance to heat and vibration |
Bushes | Excellent gap-filling properties |
Bearings | Reliable under high-temperature conditions |
Loctite 638 is also recommended for ensuring that threaded assemblies remain secure, yet can be disassembled when necessary (Loctite).
For more information on different types of adhesives, check out 1 part vs. 2 part epoxy.
Advantages of Loctite 648

Loctite 648 is engineered for precision bonding and performs exceptionally well in high-temperature applications, with effective service temperatures reaching up to 200°C (392°F) (Stickyn). This makes Loctite 648 a preferred choice for bonded heat shrink-fit assemblies and slip-fitted assemblies.
Key features of Loctite 648 include:
- Higher Temperature Tolerance: Effective up to 200°C, making it suitable for high-heat applications.
- Precision Bonding: Suitable for tasks requiring exact fit and bonding.
- Efficient Cure Speed: Ensures faster assembly processes in industrial settings.
Applications where Loctite 648 excels:
Application | Characteristics |
---|---|
Heat Shrink-Fit Assemblies | High-temp resistance and secure bonding |
Slip-Fitted Assemblies | Low-viscosity adhesive ensuring precise fit |
Press-Fitted Assemblies | Suitable for high-pressure assembly tasks |
For detailed instructions on the application of Loctite 648, Henkel Adhesives recommends applying the adhesive generously to both bond surfaces and assembling with a high press-on rate (Henkel Adhesives).
Explore other high-strength adhesives in our article on 3m super strength.
By understanding the specific advantages and recommended applications of Loctite 638 and 648, users can make informed decisions for their high-temperature and precision bonding needs. Check out our comparison of alex flex for more insights on versatile adhesives.