Loctite 603 vs. 609: Retaining Compound Guide
Comparison of Loctite Adhesives
Understanding the differences and similarities between Loctite 603 and Loctite 609 is essential for choosing the right adhesive for your specific needs. Both are high-strength retaining compounds designed for securing cylindrical fittings, but they have distinct features and applications.
Understanding Loctite 603
Loctite 603 is a high-strength retaining compound that excels in applications involving bearings and close-fitting cylindrical parts. It is known for its high oil tolerance, making it a reliable choice even in environments where oil contamination might be a concern. Loctite 603 is particularly popular in Europe for its effective performance in these specific uses (INOSAKI).
Key Features:
- High Strength: Ensures robust retention of parts.
- High Oil Tolerance: Effective even in the presence of oil contamination.
- Ideal for Close-fitting Parts: Specifically designed for bearings and cylindrical parts.
Applications commonly include securing bearings, gears, and other cylindrical parts that require a close fit. For related adhesive comparisons, explore loctite 565 vs. 567 and loctite 380 vs. 480.
Exploring Loctite 609
Loctite 609 is a high-strength acrylic retaining compound, akin to Loctite 603, but often used in the United States. It is designed for bonding cylindrical fitting parts and shares many properties with Loctite 603, such as ensuring high-strength retention. However, it is particularly noted for its medium cure speed and low viscosity, making it suitable for filling small gaps (INOSAKI). Like the Loctite 603, Loctite 609 is used extensively for retaining cylindrical fittings.
Key Features:
- High Strength: Provides strong bonding of cylindrical parts.
- Low Viscosity: Suitable for filling small gaps.
- Ideal for Cylindrical Fittings: Best used for bonding parts that fit together cylindrically.
Applications commonly include bonding bushings, pins, and other cylindrical parts that need a strong, reliable hold. For more comparisons, see loctite 609 vs. 680 and loctite 638 vs. 680.
Comparison Table
Feature | Loctite 603 | Loctite 609 |
---|---|---|
Strength | High | High |
Oil Tolerance | High | Medium |
Viscosity | Medium | Low |
Cure Speed | Medium | Medium |
Ideal Applications | Bearings, close-fitting cylindrical parts | Cylindrical fittings, bushings, pins |
Both Loctite 603 and Loctite 609 are designed to provide high-strength retention for cylindrical parts, but their unique properties make them suitable for different specific applications. Carefully consider the specific requirements of your project when choosing between these two retaining compounds.
For more insights, check out other comparisons such as contact cement vs wood glue and structural adhesive vs. welding.
Features of Loctite 603
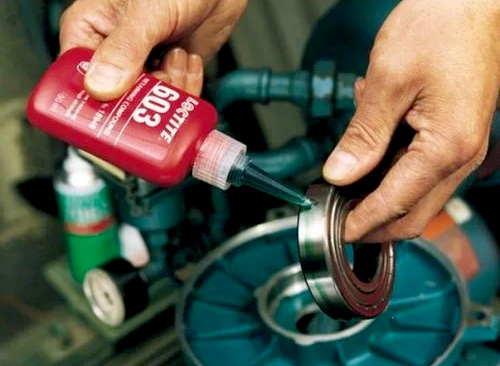
When it comes to retaining compounds, Loctite 603 stands out for its unique features and applications. Below, we delve into the strengths and various uses of Loctite 603.
Strengths of Loctite 603
Loctite 603 is renowned for its high-strength bonding capabilities, making it an excellent choice for securing bearings and close-fitting cylindrical parts. Its oil tolerance is a notable feature, allowing it to bond well even in environments where surfaces might not be perfectly clean (INOSAKI).
Feature | Description |
---|---|
Bonding Strength | High strength, ideal for heavy-duty applications |
Oil Tolerance | Performs well even on slightly oily surfaces |
Temperature Resistance | Effective within a broad temperature range |
Viscosity | Low viscosity for easy application in tight spaces |
Applications of Loctite 603
Loctite 603 is specifically designed for retaining applications, offering reliable performance in various settings. Here are some of its common applications:
Application | Description |
---|---|
Bearings | Ideal for retaining bearings in housing or shafts |
Cylindrical Parts | Effective for close-fitting cylindrical components |
Automotive | Used in securing engine and transmission parts |
Machinery | Ensures reliable assembly and maintenance of industrial machinery |
The versatility and reliability of Loctite 603 make it a preferred choice among both hobbyists and professionals. For more in-depth comparisons, check out our coverage on loctite 380 vs. 480 and loctite 565 vs. 567.
Understanding the strengths and applications of Loctite 603 can help users make informed decisions for their specific needs. When comparing with other adhesives, such as Loctite 609, it’s essential to consider these features to choose the best solution for the job at hand.
Features of Loctite 609
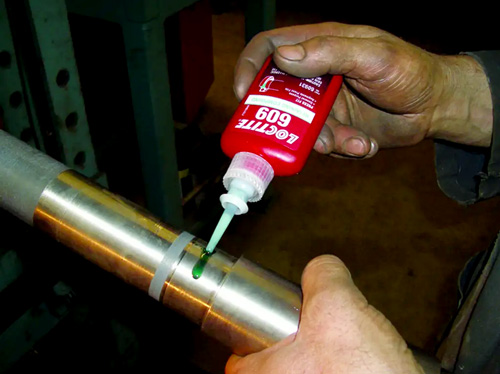
Loctite 609 is renowned for its effective bonding capabilities, making it ideal for various applications. This section will explore the strengths and uses of Loctite 609, highlighting why it is a preferred choice among adhesives.
Strengths of Loctite 609
Loctite 609 boasts several key strengths that make it a reliable retaining compound:
- High Strength: Loctite 609 provides strong adhesion for bonding cylindrical parts, ensuring durability and stability (Henkel Adhesives).
- Temperature Resistance: It can withstand temperatures ranging from -65°F to 300°F (-54°C to 150°C), making it suitable for diverse environments.
- Chemical Resistance: Offers excellent resistance to chemicals, oils, and solvents, which helps in maintaining the bond under harsh conditions.
- Sealing Properties: Effective in sealing small gaps and voids, preventing leakage and enhancing the stability of assembled parts.
Feature | Loctite 609 |
---|---|
Maximum Temperature | 300°F (150°C) |
Chemical Resistance | Excellent |
Typical Applications | Cylindrical parts |
Sealant Properties | High |
Applications of Loctite 609
Loctite 609 is suitable for various industrial and maintenance applications, including:
- Bearing Retention: Ensures tight bonds for bearings by filling voids and preventing failures.
- Sleeve and Bushing Bonding: Ideal for positioning sleeves and bushings in housings and shafts.
- Gear and Pulley Mounting: Provides strong and durable bonding for gears and pulleys on shafts.
- Rotor to Shaft Assembly: Secures rotors to shafts, preventing loosening or misalignment.
In addition to these applications, Loctite 609 is frequently used in the automotive, manufacturing, and electrical industries for its reliability and strength. For more information on other adhesives, you can explore comparisons like loctite 380 vs. 480 and loctite 565 vs. 567.
Understanding the strengths and applications of Loctite 609 can help users make informed decisions for their specific needs. For further insights into adhesive comparisons, check out loctite 609 vs. 680 and other related content.